Giving safety due weight in trade-offs
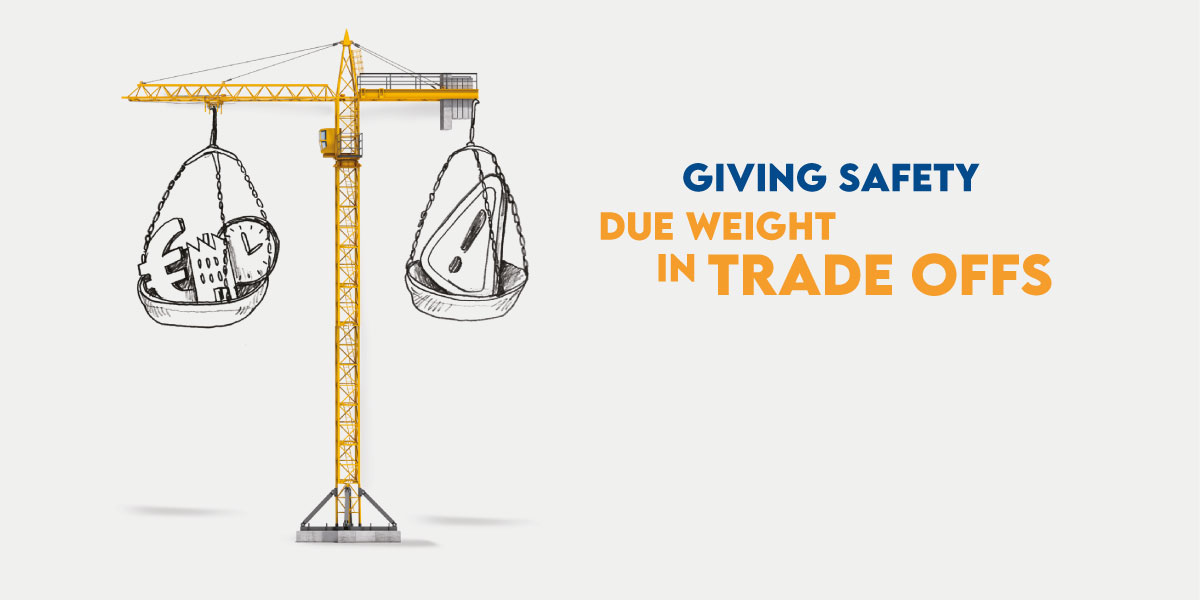
Many factors play a role in the sustainability of a company: quality, markets, deadlines, regulations... and, of course, safety, is another. Deciding which of these challenges should be given priority is a key aspect of not only the manager’s job, but also all of the organization’s actors. ‘Giving safety due weight in trade-offs’ is the third principle of strong safety leadership.
Why is it important?
An organization is subject to multiple constraints, and new scenarios emerge every day: time pressure from a customer, a technical malfunction, a lost market, workforce shortages... Every day, managers face the same question: ‘What is the most immediate and critical threat to the company? Is it a financial or commercial risk, or the risk of an accident?’ And the answer is never the same. Every day there are new trade-offs, and compromises must be made with respect to the challenges that do not take priority on the day.
Giving safety due weight’ makes it possible to:
- Move away from the maximalist idea of ‘safety first’, which is too far removed from reality and, ultimately, not very credible. In the field, trade-offs must be made, and safety is part of the equation. Instead of trying to ignore their existence, we must provide teams with the best possible support so that they can make the best possible trade-offs.
- Ensure that a trade-off never undermines safety to an unacceptable level. Safety requirements must be taken into account in managerial decisions at all levels: from managers, to functional departments, operators in the field, service providers, etc.

Can productivity and safety go hand-in-hand?
There is a mistaken belief that it is impossible to make both productivity and safety a priority; prioritizing one is thought to always be at the expense of the other. This is not true! Making safety a priority is an asset for the company, and helps it to thrive. “Of course, you have to recognize that you have to produce, but you have to produce safely. Otherwise, someone will be hurt. And downtime will cost the company. Someone who is concerned about a safety issue needs to be able to say, ‘Let’s stop for a while. Let’s fix this problem.’ It takes a few minutes, maybe more depending on the case, but the problem is fixed. When in doubt, safety must come first.”.
Dominic Cooper, B-Safe Management Solutions (USA)
How can we give safety due weight in trade-offs?
Trade-offs require us to put anything that can wait until tomorrow on the back burner. But, when it comes to safety, this isn’t easy. This is when the question of margins enters into the equation: has the organization thought about margins, where they are, and what they look like in the field?
Trade-offs that consciously compromise safety should not necessarily be avoided. Of course, no-one wants to intentionally degrade safety. But when taking decisions about other challenges, it is possible that the consequences for safety may be poorly assessed and, therefore, poorly anticipated. Let’s take the example of the decision to assign fewer workers to a task, because they are needed to support another critical activity: have the impacts in terms of safety, skills, and fatigue been thought through?
The aim of a delay must be to maintain safety at a satisfactory level, despite any compromises that must be made. Then, it becomes a question of identifying compensatory measures: ‘I can delay things if...’. Examples of compensatory measures include:
- modifications to staffing, deadlines, workloads or schedules
- full compliance with the rules, increased supervision
- close attention to the composition of teams, who must have a certain level of experience and/or expertise
- additional equipment
- increased attention to safety rituals, briefings, debriefings, safety visits, etc.
- an efficient alert system: information feedback, reports, etc.
7 recommendations for managing trade-offs
- Be prepared to make trade-offs: acknowledge that they are an integral principle of risk management
- Explain the trade-off: clearly list the different challenges, determine today’s priority, assess the potential impact on requirements associated with other challenges,
- Positively discriminate in favor of safety: assess the potential impacts of the trade-off on safety, identify any losses and gains. Commit to respecting any ‘no-go’ situations.
- Share the details of trade-offs: communicate clearly to not only supervisors, but also the teams that will have to manage the situation that results from the trade-offs that are made
- Support teams: train and assist the managers and the teams who are affected by the implementation of the trade-off
- Keep track of trade-offs: keep a record of the trade-offs that have been made to avoid an accumulation of safety concessions over too long a period
- Take a step back, and look again at the trade-offs that have been made: evaluate the process that led to the trade-off in order to take better decisions next time a trade-off needs to be made
The leader plays an essential role in helping the team find the most acceptable compromise, and to increase the weight given to safety. The role of the leader is to:
- Ensure that safety is not just a slogan, and that it is taken into account in all trade-offs, decisions and actions
- Communicate with teams, explain trade-offs, and any compensatory measures put in place
- Underline that everyone has a part to play in the co-construction safety, involve workers and service providers
- Demonstrate, through listening and your actions, the importance given to conditions on the ground
- Identify any obstacles to achieving safety objectives, then remove them
The pressure to produce is often difficult to resist. But care must be taken to maintain a minimum level of safety. To do this, you must establish ‘no-go’ rules—lines that cannot be crossed. And you must ensure that they are respected. These no-go rules should be:
- Explicit and establish criteria that determine when it is necessary to look for additional resources,
- Shared, in order to be able to stop operations before the situation degenerates,
- Accepted and respected even when stopping does not clearly reveal a problem.
---
| Read more about the 7 principles of safety leadership |